Conrad Digital Thermometer Module With LED Display Kit 192147 Data Sheet
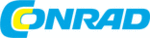
Product codes
192147
2.
Only electronic tin SN 60 Pb (i.e. 60% tin, 40% lead) with a colophony core may be
used as soldering material, which at the same time also acts as soldering flux.
used as soldering material, which at the same time also acts as soldering flux.
3.
Use a small soldering iron with max. 30 watt heating power. The soldering tip should
be tinder-free, so that the heat can be discharged properly. This means: The heat
from the soldering iron must be conducted properly to the point to be soldered.
be tinder-free, so that the heat can be discharged properly. This means: The heat
from the soldering iron must be conducted properly to the point to be soldered.
4.
The soldering itself should be done quickly, because a longer duration of soldering
can damage the components. Similarly, it also leads to release of eyelets or copper
pathways.
can damage the components. Similarly, it also leads to release of eyelets or copper
pathways.
5.
For soldering the properly tinned soldering plate is kept on the point to be soldered in
such a way that it touches the component wire and the conducting pathway at the
same time.
such a way that it touches the component wire and the conducting pathway at the
same time.
Simultaneously, soldering tin (not very much) is added, which also gets heated up.
As soon as the soldering tin starts to flow, take it away from the solder joint. Then
wait for a moment, till the solder left behind has blended properly and then remove
the soldering iron from the solder joint.
As soon as the soldering tin starts to flow, take it away from the solder joint. Then
wait for a moment, till the solder left behind has blended properly and then remove
the soldering iron from the solder joint.
6.
See to it that the component you have just soldered is not moved for approx. 5
seconds after you remove the soldering iron. What remains after that is a silvery
shining, smooth solder joint.
seconds after you remove the soldering iron. What remains after that is a silvery
shining, smooth solder joint.
7.
A prerequisite for a smooth solder joint and good soldering is a clean, non-oxidised
soldering tip. With a dirty tip it is absolutely not possible to do a clean soldering.
Therefore, after every soldering, wipe away the extra soldering tin and dirt with a
damp sponge or with a silicone wiper.
soldering tip. With a dirty tip it is absolutely not possible to do a clean soldering.
Therefore, after every soldering, wipe away the extra soldering tin and dirt with a
damp sponge or with a silicone wiper.
8.
After soldering the connection wires are cut directly above the solder joint with a wire
cutter.
cutter.
9.
When soldering semi-conductors, LEDs and ICs special attention must be paid to the
fact that the soldering time does not exceed approx. 5 seconds, as otherwise the
component gets destroyed. Similarly, attention must also be paid to the correct
polarity in case of these components.
fact that the soldering time does not exceed approx. 5 seconds, as otherwise the
component gets destroyed. Similarly, attention must also be paid to the correct
polarity in case of these components.
10.
After mounting, check each circuit once again to see that all components are
inserted correctly and polarised. Also check, whether the connections or conducting
pathways have not been bridged by mistake with tin. This can not only lead to faulty
functioning, but also to a damage of the expensive components.
inserted correctly and polarised. Also check, whether the connections or conducting
pathways have not been bridged by mistake with tin. This can not only lead to faulty
functioning, but also to a damage of the expensive components.
11.
Please note that improper solder joints, false connections, improper usage and
mounting faults are outside of our influence.
mounting faults are outside of our influence.
1. Construction stage I:
Mounting the components on the printed circuit board
1.1 Resistors
First, the connection wires of the resistors are bent at right angles conforming to the
contact spacing and inserted in the openings provided (as per the component diagram).
In order that the components do not fall out when the board is turned over, bend the
connection wires of the resistors away from one another at an angle of approx. 45°, and
then solder them carefully with the conducting pathways on the rear side of the printed
circuit board.
contact spacing and inserted in the openings provided (as per the component diagram).
In order that the components do not fall out when the board is turned over, bend the
connection wires of the resistors away from one another at an angle of approx. 45°, and
then solder them carefully with the conducting pathways on the rear side of the printed
circuit board.