Idec RF1V-5A1BL-D24 PCB Mount Relay 5 NO / 1 NC RF1V-5A1BL-D24 User Manual
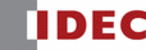
Product codes
RF1V-5A1BL-D24
2
Force guided contact mechanism
(EN50205 Type A TÜV approved)
Complies with International Standards
Response time of 8 ms.
Ensures safety by turning the load off quickly.
(200 m/s
2
minimum)
Fast Response Time
High shock resistant suitable for use in machine tools and in
environments subjected to vibration and shocks.
High Shock Resistance
Available with a built-in LED.
Clear Visiblilty
Compact size enables size reduction of PC board.
4-pole type: 13W × 40D × 24H mm
6-pole type: 13W × 50D × 24H mm
Compact and Slim
PC board mount and DIN rail mount sockets are available.
Socket Variation
PC board mount
DIN rail mount
Applications
Output expansion for safety relay modules and safety controllers
Contacts of a force guided relay are forced to open and
close by a guide connected to the armature.
Due to requirements of standard EN50205, a force guided
relay has independent NO and NC contacts. If a NO con-
tact welds, a NC contact will not close even when the relay
coil is turned off (de-energized) and must maintain a gap of
at least 0.5 mm. Furthermore, if a NC contact welds, a NO
contact will not close when the relay is turned on (ener-
gized) and must maintain a gap of at least 0.5 mm.
(General-purpose relays do not have the above characteristics.)
What is a force guided relay?
Relays used in safety circuits to detect failures such as contact welding and damage to the
contact spring.
Circuit Example
•
Circuit Example
•
EDM input: External device monitor input
FS1A Safety Controller
•
HR1S Safety Relay Module
•
Safety Relay Module
Interlock Switch/
Emergency Stop Switch
Start
Switch
K2
K1
F1 F2
EDM Input
Safety Output Expansion
Force Guided Relays
Force Guided Relays
Force guided relays are used in safety circuits in combination with in-
terlock switches, light curtains, and emergency stop switches to control
outputs.
They can also be used to expand outputs for safety relay modules and
safety controllers.
De-energized
(Normal
Condition)
Energized
(Normal
Condition)
A gap of at least
0.5 mm is maintained
NO contact
is welded
De-energized
(Abnormal
Condition)
Energized
(Abnormal
Condition)
A gap of at least
0.5 mm is maintained
NC contact
is welded
Armature
Guide
NC
contact
NO
contact
Armature
Guide
NC
contact
NO
contact
Solid state safety outputs of safety controllers can be converted
to mechanical contact outputs.
Cost effective and easy method to expand mechanical
contact outputs.
K2
K1
24V
Interlock Switch/
Emergency Stop Switch
Start
Switch
Safety Controller
EDM Input
Safety Output Expansion
Force Guided Relays
Force Guided Relays
Guide
NC contact
NO contact
Enables flexible construction of safety circuits
(090319)