Omron C200HX Manuel D’Utilisation
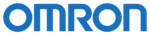
5
7. Wire the PC to the controlled system. This step can actually be started as
soon as step 3 has been completed. Refer to the C200HX/HG/HE PC Instal-
lation Guide and to Operation Manuals and System Manuals for details on
individual Units.
lation Guide and to Operation Manuals and System Manuals for details on
individual Units.
8. Test the program in an actual control situation and carry out fine tuning as
required. (Section 7 Program Monitoring and Execution and Section 9 Trou-
bleshooting)
bleshooting)
9. Record two copies of the finished program on masters and store them safely
in different locations. (Section 4-7 Inputting, Modifying, and Checking the
Program)
Program)
Control System Design
Designing the Control System is the first step in automating any process. A PC
can be programmed and operated only after the overall Control System is fully
understood. Designing the Control System requires, first of all, a thorough un-
derstanding of the system that is to be controlled. The first step in designing a
Control System is thus determining the requirements of the controlled system.
can be programmed and operated only after the overall Control System is fully
understood. Designing the Control System requires, first of all, a thorough un-
derstanding of the system that is to be controlled. The first step in designing a
Control System is thus determining the requirements of the controlled system.
Input/Output Requirements
The first thing that must be assessed is the number of input and output points
that the controlled system will require. This is done by identifying each device
that is to send an input signal to the PC or which is to receive an output signal
from the PC. Keep in mind that the number of I/O points available depends on
the configuration of the PC. Refer to 3-3 IR Area for details on I/O capacity and
the allocation of I/O bits to I/O points.
that the controlled system will require. This is done by identifying each device
that is to send an input signal to the PC or which is to receive an output signal
from the PC. Keep in mind that the number of I/O points available depends on
the configuration of the PC. Refer to 3-3 IR Area for details on I/O capacity and
the allocation of I/O bits to I/O points.
Next, determine the sequence in which control operations are to occur and the
relative timing of the operations. Identify the physical relationships between the
I/O devices as well as the kinds of responses that should occur between them.
relative timing of the operations. Identify the physical relationships between the
I/O devices as well as the kinds of responses that should occur between them.
For instance, a photoelectric switch might be functionally tied to a motor by way
of a counter within the PC. When the PC receives an input from a start switch, it
could start the motor. The PC could then stop the motor when the counter has
received a specified number of input signals from the photoelectric switch.
of a counter within the PC. When the PC receives an input from a start switch, it
could start the motor. The PC could then stop the motor when the counter has
received a specified number of input signals from the photoelectric switch.
Each of the related tasks must be similarly determined, from the beginning of the
control operation to the end.
control operation to the end.
Unit Requirements
The actual Units that will be mounted or connected to PC Racks must be deter-
mined according to the requirements of the I/O devices. Actual hardware specifi-
cations, such as voltage and current levels, as well as functional considerations,
such as those that require Special I/O Units or Link Systems will need to be con-
sidered. In many cases, Special I/O Units, Intelligent I/O Units, or Link Systems
can greatly reduce the programming burden. Details on these Units and Link
Systems are available in appropriate Operation Manuals and System Manuals.
mined according to the requirements of the I/O devices. Actual hardware specifi-
cations, such as voltage and current levels, as well as functional considerations,
such as those that require Special I/O Units or Link Systems will need to be con-
sidered. In many cases, Special I/O Units, Intelligent I/O Units, or Link Systems
can greatly reduce the programming burden. Details on these Units and Link
Systems are available in appropriate Operation Manuals and System Manuals.
Once the entire Control System has been designed, the task of programming,
debugging, and operation as described in the remaining sections of this manual
can begin.
debugging, and operation as described in the remaining sections of this manual
can begin.
1-6
Peripheral Devices
The following peripheral devices can be used in programming, either to input/
debug/monitor the PC program or to interface the PC to external devices to out-
put the program or memory area data. Model numbers for all devices listed be-
low are provided in Appendix A Standard Models. OMRON product names have
been placed in bold when introduced in the following descriptions.
debug/monitor the PC program or to interface the PC to external devices to out-
put the program or memory area data. Model numbers for all devices listed be-
low are provided in Appendix A Standard Models. OMRON product names have
been placed in bold when introduced in the following descriptions.
Programming Console
A Programming Console is the simplest form of programming device for OM-
RON PCs. All Programming Consoles are connected directly to the CPU Unit
without requiring a separate interface.
RON PCs. All Programming Consoles are connected directly to the CPU Unit
without requiring a separate interface.
SSS is designed to run on IBM PC/AT or compatibles and allows you to perform
all the operations of the Programming Console as well as many additional ones.
all the operations of the Programming Console as well as many additional ones.
Sequence, Timing, and
Relationships
Relationships
SYSMAC Support Software:
SSS
SSS
Peripheral Devices
Section 1-6