Graupner Hendheld RC 2.4 GHz No. of channels: 12 33124 데이터 시트
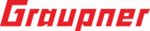
제품 코드
33124
244 Detail program description - Control adjust
Integration of an electric drive into the model programming
An electric drive can be controlled in different ways:
The simplest method to integrate one such drive into
the model programming is with the use of a throttle/
brake joystick (C1). However, since this is already
specifi ed for the brake system in the course of the model
programming described above, either the switchable
solution described beginning on page 247 or even the
use of an alternative control is possible.
As such, one of the two three-stage switches CTRL 9
or 10 is better suited than the proportional rotary control
CTRL 6 ... 8. (Unlike rotary controls, switches can be
operated with one fi nger without having to release
the joystick). An alternative would also be one of the
two-stage switches. Basically, the switch should be
positioned conveniently within reach.
Before we turn to the individual examples, it is important
must be noted that all inputs in the Control adjust menu
can be selectively programmed as fl ight-phase specifi c
("PH" in the "Type" column) or model memory specifi c
("GL" in the "Type" column)!
However, since the drive should usually be available
depending on the current fl ight phase, we recommend
leaving the standard default "GL" ("global") in the "Type"
column which your are using.
The simplest method to integrate one such drive into
the model programming is with the use of a throttle/
brake joystick (C1). However, since this is already
specifi ed for the brake system in the course of the model
programming described above, either the switchable
solution described beginning on page 247 or even the
use of an alternative control is possible.
As such, one of the two three-stage switches CTRL 9
or 10 is better suited than the proportional rotary control
CTRL 6 ... 8. (Unlike rotary controls, switches can be
operated with one fi nger without having to release
the joystick). An alternative would also be one of the
two-stage switches. Basically, the switch should be
positioned conveniently within reach.
Before we turn to the individual examples, it is important
must be noted that all inputs in the Control adjust menu
can be selectively programmed as fl ight-phase specifi c
("PH" in the "Type" column) or model memory specifi c
("GL" in the "Type" column)!
However, since the drive should usually be available
depending on the current fl ight phase, we recommend
leaving the standard default "GL" ("global") in the "Type"
column which your are using.
Input 5
offset
0%
0%
0%
0%
0%
–––
0%
Input 6
Input 7
Input 8
Input 7
Input 8
–––
–––
–––
GL
GL
GL
GL
typ
A common option in the following examples 1 ... 5, the
automatic tracking of the elevator trimming in the power
fl ight, should also be mentioned at the beginning of this
section:
If it becomes apparent after the initial power fl ights
that the model must be continuously corrected with the
elevator while the motor is switched on, this situation
can be corrected by setting a free mixer and adjusting it
accordingly. For this purpose, switch to the menu ...
automatic tracking of the elevator trimming in the power
fl ight, should also be mentioned at the beginning of this
section:
If it becomes apparent after the initial power fl ights
that the model must be continuously corrected with the
elevator while the motor is switched on, this situation
can be corrected by setting a free mixer and adjusting it
accordingly. For this purpose, switch to the menu ...
""Free mixers"
… and program one of the linear mixers M1 … 8 or, if
applicable, also one of the curve mixers K9 … 12 from
"channel controlling the motor" according to "Ele", e. g.
of "8
applicable, also one of the curve mixers K9 … 12 from
"channel controlling the motor" according to "Ele", e. g.
of "8
Ele":
typ
fr
to
M1
M2
M3
M2
M3
8
EL
M4
M5
M5
??
??
??
??
??
??
??
??
On its second screen page, the required – usually
low – correction value is entered:
low – correction value is entered:
L.MIX 1
0%
Offset
ASY
SYM
8
EL
Mix input
+4%
+4%
Notice:
The adjustment of a curve mixer is described in detail in
the section "Channel 1 curve" starting on page 116.
The adjustment of a curve mixer is described in detail in
the section "Channel 1 curve" starting on page 116.
Example 1
Use of a proportional rotary control
CTRL 6 … 8
If one of these controls is used, the connection is very
simple. Only the motor controller (speed control) has to
be connected to a free servo connection 5 ... 12 of the
receiver.
CTRL 6 … 8
If one of these controls is used, the connection is very
simple. Only the motor controller (speed control) has to
be connected to a free servo connection 5 ... 12 of the
receiver.
Bear in mind that, depending on the model type and
number of aileron and fl ap servos, the output 2 + 5 or 6
+ 7 are already linked.
number of aileron and fl ap servos, the output 2 + 5 or 6
+ 7 are already linked.
Therefore connect your speed controller to the next free
input and assign the selected input – for example, "Inp.
8" – one of the proportional rotary controls CTRL 6 ... 8.
For example, CTRL 7. This is carried out in the menu ...
input and assign the selected input – for example, "Inp.
8" – one of the proportional rotary controls CTRL 6 ... 8.
For example, CTRL 7. This is carried out in the menu ...
""Control adjust"
(page 96)
With the arrow keys
of the left or right touch pad,
select the desired line. Then, by pressing the central
SET
key of the right touch pad, you active the "Switch
and control assignment". Now turn the knob of the
proportional rotary control. After a short time, the entry,
e. g. "Control 7", appears in the inverse fi eld.
proportional rotary control. After a short time, the entry,
e. g. "Control 7", appears in the inverse fi eld.