ParkZone Radian RTF PKZ4700 Data Sheet
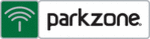
Product codes
PKZ4700
12
SPEKTRUM DX5e • RADIO USER’S GUIDE
13
SPEKTRUM DX5e • RADIO USER’S GUIDE
3. If using a regulator, it’s important the above tests are
done for an extended period of 5 minutes. When current
passes through a regulator, heat is generated. This
heat causes the regulator to increase resistance, which
in turn causes even more heat to build up (thermal
runaway). While a regulator may provide adequate
power for a short duration, it’s important to test its
ability over time as the regulator may not be able to
maintain voltage at significant power levels.
4. For really large aircraft or complex models (for example
35% and larger or jets), multiple battery packs with
multiple switch harnesses are necessary or in many
cases one of the commercially available power boxes/
busses is recommended. No matter what power systems
you choose, always carry out test #1 above making sure
that the receiver is constantly provided with 4.8 volts or
more under all conditions.
5. The latest generation of Nickel-Metal Hydride batteries
incorporates a new chemistry mandated to be more
environmentally friendly. These batteries, when charged
with peak detection fast chargers, have a tendency to
false peak (not fully charge) repeatedly. These include
all brands of NiMH batteries. If using NiMH packs be
especially cautious when charging making absolutely
sure that the battery is fully charged. It is recommended
to use a charger that can display total charge capacity.
Note the number of mAh put into a discharged pack to
verify it has been charged to full capacity.
TIPS On USInG 2.4Ghz SySTEMS
Your DSM2 equipped 2.4GHz system is intuitive to operate,
functioning nearly identically to FM systems. Following are
a few common questions from customers:
1. Q: Which do I turn on first, the transmitter or the
receiver?
A: It doesn’t matter, although it is suggested to turn the
transmitter on first. If the receiver is turned on first,
the throttle channel doesn’t put out a pulse position at
this time, preventing the arming of electronic speed
controllers, or in the case of an engine powered aircraft,
the throttle servo remains in its current position. When
the transmitter is then turned on the transmitter scans
the 2.4GHz band and acquires two open channels. Then
the receiver that was previously bound to the transmitter
scans the band and finds the GUID (Globally Unique
Identifier code) stored during binding. The system then
connects and operates normally. If the transmitter is
turned on first, the transmitter scans the 2.4GHz band
and acquires two open channels. When the receiver
is turned on, the receiver scans the 2.4GHz band
looking for the previously stored GUID. When it locates
the specific GUID code and confirms uncorrupted
repeatable packet information, the system connects and
normal operation takes place. Typically this takes 2 to 6
seconds.
2. Q: Sometimes the system takes longer to connect and
sometimes it doesn’t connect at all. Why?
A In order for the system to connect (after the receiver is
bound), the receiver must receive a large number of
continuous (one after the other) uninterrupted perfect
packets from the transmitter. This process is purposely
critical of the environment ensuring that it’s safe to fly
when the system does connect. If the transmitter is too
close to the receiver (less that 4 feet) or if the transmitter
is located near metal objects (metal transmitter case,
the bed of a truck, the top of a metal work bench, etc.)
connection will take longer. In some cases connection
will not occur as the system is receiving reflected
2.4GHz energy from itself and is interpreting this
as unfriendly noise. Moving the system away from
metal objects or moving the transmitter away from the
receiver and powering the system up again will cause
a connection to occur. This only happens during the
initial connection. Once connected the system is locked,
and should a loss of signal occur (failsafe), the system
connects immediately (4ms) when signal is regained.
3. Q: I’ve heard that the DSM system is less tolerant of low
voltage. Is this correct?
A: All DSM receivers have an operational voltage range of
3.5 to 9 volts. With most systems this is not a problem
as in fact most servos cease to operate at around 3.8
volts. When using multiple high-current draw servos
with a single or inadequate battery/ power source, heavy
momentary loads can cause the voltage to dip below
this 3.5-volt threshold causing the entire system (servos
and receiver) to brown out. When the voltage drops
below the low voltage threshold (3.5 volts), the DSM
receiver must reboot (go through the start up process of
scanning the band and finding the transmitter) and this
can take several seconds.
4. Q: Sometimes my receiver loses its bind and won’t
connect, requiring rebinding. What happens if the bind
is lost in flight?
A: The receiver will never lose its bind unless it’s instructed
to. It’s important to understand that during the binding
process the receiver not only learns the GUID (code) of
the transmitter but the transmitter learns and stores the
type of receiver that it’s bound to. If the trainer switch is
pulled on the transmitter at any time and the transmitter
is turned on, the transmitter looks for the binding
protocol signal from a receiver. If no signal is present,
the transmitter no longer has the correct information
to connect to a specific receiver and in essence the
transmitter has been “unbound” from the receiver. We’ve
had several customers using transmitter stands or trays
that unknowingly depress the bind button. The system
is then turned on, losing the necessary information
to allow the connection to take place. We’ve also had
customers that didn’t fully understand the range test
process and pull the trainer switch before turning on the
transmitter, also causing the system to “lose its bind.”
If the system fails to connect, one of the following has
occurred:
• The transmitter is near conductive material (transmitter
case, truck bed, etc.) and the reflected 2.4GHz energy is
preventing the system from connecting. (See #2 above)
• The trainer switch was pulled and the radio was
previously turned on knowingly (or unknowingly),
causing the transmitter to no longer recognize the
receiver.
GEnERAl InfORMATIOn
FCC Information
This device complies with part 15 of the FCC rules.
Operation is subject to the following two conditions: (1)
This device may not cause harmful interference, and (2)
this device must accept any interference received, including
interference that may cause undesired operation.
Caution: Changes or modifications not expressly
approved by the party responsible for compliance could
void the user’s authority to operate the equipment.
This product contains a radio transmitter with wireless
technology which has been tested and found to be compliant
with the applicable regulations governing a radio transmitter
in the 2.400GHz to 2.4835GHz frequency range.
Servo Precautions
• Do not lubricate servo gears or motors.
• Do not overload retract servos during retracted or
• Do not overload retract servos during retracted or
extended conditions. Make sure they are able to
travel their full deflection. Overloading or stalling a
servo can cause excessive current drain.
• Make sure all servos move freely through their
rotations and no linkages hang up or bind. A binding
control linkage can cause a servo to draw excessive
current. A stalled servo can drain a battery pack in a
matter of minutes.
• Correct any control surface “buzz” or “flutter” as soon
as it is noticed in flight, as this condition can destroy
the feedback potentiometer in the servo. It may be
extremely dangerous to ignore such “buzz” or “flutter.”
• Use the supplied rubber grommets and brass servo
eyelets when mounting your servos. Do not over-
tighten the servo mounting screws, as this negates the
dampening effect of the rubber grommets.
• Ensure the servo horn is securely fastened to the servo.
Use only the servo arm screws provided; the size is
different from other manufacturers.
• Discontinue to use servo arms when they become
“yellowed” or discolored. Such servo arms may be
brittle and can snap at any time, possibly causing the
aircraft to crash.
• Check all related mounting screws and linkages
frequently. Aircraft often vibrate, causing linkages and
screws to loosen.