Braun Mobility Aid RA200 Manuale Utente
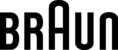
Page 9
in the controller during installa-
tion immediately stops move-
ment when obstructed. Once an
obstruction has halted the ramp,
the controller automatically resets
and awaits operator input for
further operation.
tion immediately stops move-
ment when obstructed. Once an
obstruction has halted the ramp,
the controller automatically resets
and awaits operator input for
further operation.
Note: The ramp will sense an
obstruction and halt with any
substantial weight on the platform
(built-in safety feature). The ramp
will continue when the weight is
removed from platform.
obstruction and halt with any
substantial weight on the platform
(built-in safety feature). The ramp
will continue when the weight is
removed from platform.
Operation Functionality
The 100465-002 easy ramp con-
trol box incorporates a Microchip
PIC microcontroller that executes
a sequential program from a
built-in flash memory. This sec-
tion gives a brief overview of the
operational functionality that the
firmware provides in the operation
of the ramp.
trol box incorporates a Microchip
PIC microcontroller that executes
a sequential program from a
built-in flash memory. This sec-
tion gives a brief overview of the
operational functionality that the
firmware provides in the operation
of the ramp.
One-Touch Operation: A mo-
mentary pulse input from an oper-
ate button will start an automated
deployment sequence. The user
does not have to continue to
press the operate button for the
ramp to complete its motion. In
a similar manner, the user need
only push the operate button once
again to start a stow sequence.
mentary pulse input from an oper-
ate button will start an automated
deployment sequence. The user
does not have to continue to
press the operate button for the
ramp to complete its motion. In
a similar manner, the user need
only push the operate button once
again to start a stow sequence.
Ramp Enable: The ramp must
first be enabled by applying a mo-
mentary pulse signal to the ramp
enable input (momentary push-
button switch). Once enabled,
the “Ramp Enabled” normally
open (N.O.) output is activated.
Then, the ramp may be operated
using the “Ramp Operate” button.
The ramp is automatically dis-
abled when the platform becomes
fully stowed at the end of a cycle.
The ramp may also be disabled if
the enable push-button is pressed
again.
first be enabled by applying a mo-
mentary pulse signal to the ramp
enable input (momentary push-
button switch). Once enabled,
the “Ramp Enabled” normally
open (N.O.) output is activated.
Then, the ramp may be operated
using the “Ramp Operate” button.
The ramp is automatically dis-
abled when the platform becomes
fully stowed at the end of a cycle.
The ramp may also be disabled if
the enable push-button is pressed
again.
“Close All Doors” Input: An
optional input, “Close All Doors,”
may be used to cause a stow
sequence. This input is also a
momentary pulse input. At the
completion of a stow cycle, the
control box will de-activate the
“Open Door” output. The door
should then automatically close.
optional input, “Close All Doors,”
may be used to cause a stow
sequence. This input is also a
momentary pulse input. At the
completion of a stow cycle, the
control box will de-activate the
“Open Door” output. The door
should then automatically close.
Opening Door: The control box
opens the door using the “Open
Door” output. For the duration of
the ramp deployment and stow
cycle, the door shall never be al-
lowed to close. At the completion
of a stow cycle, the control box
will de-activate the “Open Door”
output. The door may automati-
cally close or close after the driver
signals the door to close.
If the door fails to open after an 8
second timeout period, the “Open
Door” output will be deactivated
and the ramp will not be de-
ployed.
opens the door using the “Open
Door” output. For the duration of
the ramp deployment and stow
cycle, the door shall never be al-
lowed to close. At the completion
of a stow cycle, the control box
will de-activate the “Open Door”
output. The door may automati-
cally close or close after the driver
signals the door to close.
If the door fails to open after an 8
second timeout period, the “Open
Door” output will be deactivated
and the ramp will not be de-
ployed.
Obstruction Sensing: The
control box can sense if the ramp
platform is obstructed during
movement using a pressure mat
and over-current circuitry. If one
of these detection techniques oc-
curs, the ramp is halted. If three
consecutive obstructions during
the deployment cycle occur, the
auto-stow feature described in
Section 3.10 will execute.
control box can sense if the ramp
platform is obstructed during
movement using a pressure mat
and over-current circuitry. If one
of these detection techniques oc-
curs, the ramp is halted. If three
consecutive obstructions during
the deployment cycle occur, the
auto-stow feature described in
Section 3.10 will execute.
Pressure Mat Detection: The
top surface of the ramp platform
is covered with a weight or pres-
sure sensitive mat. If a pas-
senger is on top of the platform,
the ramp will not move when
activated. If the ramp is already
in motion and weight is applied to
the platform, the ramp will halt its
motion. Additionally, the platform
may be equipped with a pressure
sensitive edge strip that senses
obstructions at the leading edge.
top surface of the ramp platform
is covered with a weight or pres-
sure sensitive mat. If a pas-
senger is on top of the platform,
the ramp will not move when
activated. If the ramp is already
in motion and weight is applied to
the platform, the ramp will halt its
motion. Additionally, the platform
may be equipped with a pressure
sensitive edge strip that senses
obstructions at the leading edge.
The leading edge ovstruction strip
would be wired with the pressure
mat and therefore behave simi-
larly.
would be wired with the pressure
mat and therefore behave simi-
larly.
Ramp Alarm: Prior to any mo-
tion of the ramp, an alarm output
is activated for a few seconds.
The alarm output sounds for the
duration that the ramp platform is
not fully deployed or fully stowed.
This continuous output is used to
power an audible alarm and/or
lights. For the lights to flash, a
special harness (ER1320A) is
used with a built-in flashing unit.
tion of the ramp, an alarm output
is activated for a few seconds.
The alarm output sounds for the
duration that the ramp platform is
not fully deployed or fully stowed.
This continuous output is used to
power an audible alarm and/or
lights. For the lights to flash, a
special harness (ER1320A) is
used with a built-in flashing unit.
Operation