Spektrum DX6i SPM6630 用户手册
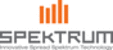
产品代码
SPM6630
20
SPEKTRUM DX6i • RADIO INSTRUCTION MANUAL
EN
In airplanes, install the main receiver in the servo tray in the cen-
ter of the fuselage. Install the remote receiver in the servo tray
by the side of the fuselage or in the turtle deck (space behind
the canopy and in front of the vertical stabilizer).
ter of the fuselage. Install the remote receiver in the servo tray
by the side of the fuselage or in the turtle deck (space behind
the canopy and in front of the vertical stabilizer).
In helicopters, install receivers in the servo tray, where there
is usually sufficient room for receiver separation. Where there
is not sufficient room, install a receiver on an external receiver
mount made of clear plastic.
Note: The DSMX DX6i is compatible with all current Spektrum
DSM2 and DSMX aircraft receivers, but NOT compatible with the
original DSM AR6000 receiver.
is usually sufficient room for receiver separation. Where there
is not sufficient room, install a receiver on an external receiver
mount made of clear plastic.
Note: The DSMX DX6i is compatible with all current Spektrum
DSM2 and DSMX aircraft receivers, but NOT compatible with the
original DSM AR6000 receiver.
CAUTION: When using the DSMX DX6i with parkflyer
receivers (the AR6100, AR6110, and AR6115), it’s
receivers (the AR6100, AR6110, and AR6115), it’s
imperative that these receivers only be flown in parkflyer-type
aircraft (small electric airplanes or mini and micro helicopters).
Flying receivers designed for parkflyers in larger aircraft could
cause loss of connection.
aircraft (small electric airplanes or mini and micro helicopters).
Flying receivers designed for parkflyers in larger aircraft could
cause loss of connection.
Servo Installation
Due to vibration, install servos using rubber grommets and
bushings in gas- and glow-powered models.
bushings in gas- and glow-powered models.
Do not over-tighten mounting screws.
Install servos using servo tape and glue in electric and non-
powered aircraft. See model instructions for installing servo(s)
in your model.
Install servos using servo tape and glue in electric and non-
powered aircraft. See model instructions for installing servo(s)
in your model.
Servo Precautions
Do NOT lubricate servo gears or motors.
Do NOT overload retract servos during retracted or extended
conditions.
conditions.
Always make sure servo arms and linkages can move freely over
the whole path of their intended travel. A blocked servo linkage
or servo arm can cause a servo to draw too much current so a
battery charge is quickly drained.
the whole path of their intended travel. A blocked servo linkage
or servo arm can cause a servo to draw too much current so a
battery charge is quickly drained.
Always correct control surface vibration, such as “buzz” or “flut-
ter.” Vibration can destroy feedback potentiometers in servos.
ter.” Vibration can destroy feedback potentiometers in servos.
Always install servos using rubber grommets and brass eyelets.
Do NOT over-tighten servo mounting screws. Doing so inhibits
the screws from dampening vibration.
Do NOT over-tighten servo mounting screws. Doing so inhibits
the screws from dampening vibration.
Always make sure a servo arm is fully attached to the servo. Use
only supplied servo arm screws. Use of other sizes of screws or
screws from other manufacturers can result in damage to the
servo.
only supplied servo arm screws. Use of other sizes of screws or
screws from other manufacturers can result in damage to the
servo.
Always remove and discard “yellowed” or otherwise discolored
servo arms. Discoloration shows material may be brittle and can
break at any time, possibly causing an aircraft crash.
servo arms. Discoloration shows material may be brittle and can
break at any time, possibly causing an aircraft crash.
Always make sure model screws and linkages are tight. Vibration
loosens screws and linkages so that damage can result.
loosens screws and linkages so that damage can result.
Power System Requirements
Set up and operate a model so power to the receiver is NEVER
interrupted while flying. This is especially critical on giant-scale
models that use several high-torque or high-current servos.
Power systems unable to provide minimum receiver voltage
in flight are the number-one cause of in-flight failures. Some
interrupted while flying. This is especially critical on giant-scale
models that use several high-torque or high-current servos.
Power systems unable to provide minimum receiver voltage
in flight are the number-one cause of in-flight failures. Some
components that cause a receiver to have too little power supply
include:
include:
• Receiver battery (number of cells, capacity, cell type, state of
charge)
• Switch harness
• Battery leads
• Regulator (where used),
• Power bus (where used)
• Battery leads
• Regulator (where used),
• Power bus (where used)
While a Spektrum receiver’s minimum operational voltage is
3.5 volts, test your model to a minimum acceptable voltage of
4.8 volts during ground testing. This battery charge capacity
compensates for discharge during flight or for flight loads larger
than ground test loads.
3.5 volts, test your model to a minimum acceptable voltage of
4.8 volts during ground testing. This battery charge capacity
compensates for discharge during flight or for flight loads larger
than ground test loads.
CAUTION: We recommend that you DO NOT fly a model
with battery charges at less than 5.3-volts.
with battery charges at less than 5.3-volts.
Recommended Power System Guidelines
1. When setting up a large or complex aircraft with multiple
high-torque servos, use a current and voltmeter (Hangar 9
HAN172). Connect the volt-meter in an open channel port in
the receiver. With the system powered on, load the control
surfaces (apply pressure with your hand) while monitoring
voltage at the receiver. The voltage must remain above 4.8
volts when all servos are heavily loaded.
HAN172). Connect the volt-meter in an open channel port in
the receiver. With the system powered on, load the control
surfaces (apply pressure with your hand) while monitoring
voltage at the receiver. The voltage must remain above 4.8
volts when all servos are heavily loaded.
Note: The optional Spektrum Flight Log (SPM9540) has a
built-in voltmeter for doing this test. The Flight Log is compat-
ible with Spektrum receivers SPMAR9010, SPMAR9110 and
SPMAR7010 (AR7000).
built-in voltmeter for doing this test. The Flight Log is compat-
ible with Spektrum receivers SPMAR9010, SPMAR9110 and
SPMAR7010 (AR7000).
2. With the current meter connected in line with the receiver
battery lead, load control surfaces (apply pressure with your
hand) while monitoring the current. The maximum continu-
ous current for a single heavy-duty servo/battery lead must
be no more than 3 amps, while short-duration current spikes
of up to 5 amps are acceptable. When your system draws
more than 3 amps continuous or 5 amps for short durations,
use multiple packs with multiple switches and multiple leads
connected to the receiver.
hand) while monitoring the current. The maximum continu-
ous current for a single heavy-duty servo/battery lead must
be no more than 3 amps, while short-duration current spikes
of up to 5 amps are acceptable. When your system draws
more than 3 amps continuous or 5 amps for short durations,
use multiple packs with multiple switches and multiple leads
connected to the receiver.
Note: The Flight Log cannot measure current draw (amps).
When the Flight Log is used to measure voltage, also use the
HAN172 current meter to measure the current draw of the
servos.
When the Flight Log is used to measure voltage, also use the
HAN172 current meter to measure the current draw of the
servos.
3. When using a voltage regulator, do the tests for 5 minutes or
more. Current passing through a regulator generates heat.
Resistance increases, causing heat to increase (thermal
runaway). While a regulator may provide adequate power for
a short time, test for longer to make sure it can keep voltage
consistent at significant power levels.
Resistance increases, causing heat to increase (thermal
runaway). While a regulator may provide adequate power for
a short time, test for longer to make sure it can keep voltage
consistent at significant power levels.
4. Use multiple battery packs with multiple switch harnesses
on large aircraft or complex models (for example, airplanes
35% and larger or jets). In many cases, commercially avail-
able power boxes or busses must be used. No matter what
power systems are used, always do a test (described above)
to make sure the receiver is supplied with 4.8 volts or more
under all conditions.
35% and larger or jets). In many cases, commercially avail-
able power boxes or busses must be used. No matter what
power systems are used, always do a test (described above)
to make sure the receiver is supplied with 4.8 volts or more
under all conditions.
5. Peak detection fast chargers may show a false full charge on
NiMH batteries. We recommend use of a charger that shows
an NiMH battery’s total charge capacity. Make sure NiMH
battery packs are fully charged when using any charger.
an NiMH battery’s total charge capacity. Make sure NiMH
battery packs are fully charged when using any charger.